Practical Use Cases
What Do Lean Operations Consultants Do?
Identifying Waste in Operations
Redesigning Process Flows
Implementing Lean Tools
Hire Lean Operations Consultants,
Easier than Ever Before
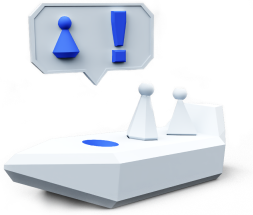
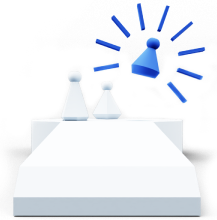
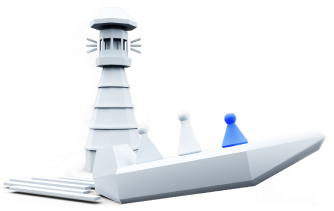
FAQs

What makes Lean Operations Consultants different?

Is hiring Lean Operations Consultants through Consultport in less than 48 hours possible?

What does the βno-risk, pay only if satisfiedβ mean when I search for Lean Operations Consultants?
Ready to get started?
Why Hire Lean Operations Consultants?
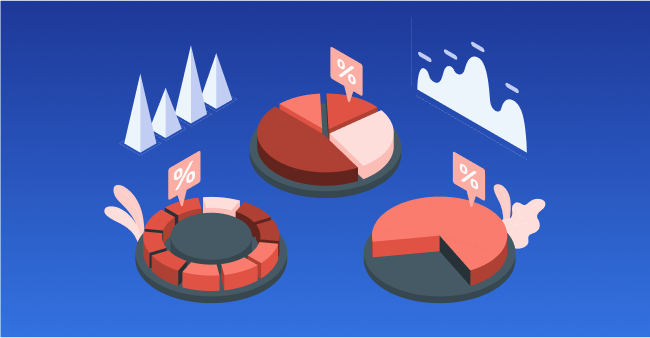
When it comes to integrating lean operations with current processes, over 70% of companies fail to deliver the expected outcomes due to misaligned practices, inconsistent execution, and lack of expertise.
This is where Lean Operations Consultants add critical value. They bring specialized knowledge in lean methodologies, helping businesses streamline operations, reduce waste, and improve overall efficiency. Lean consultants focus on company-specific issues, ensuring that every process improvement initiative is aligned with operational goals and designed for long-term sustainability.
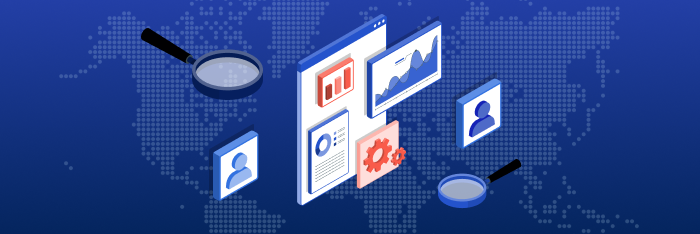
Our platform connects you with top-tier Lean Operations Consultants who can help transform your business. Here are key areas where they drive meaningful improvements:
Reducing Operational Waste
Consultants use lean tools like value stream mapping and root cause analysis to eliminate non-value-adding activities, cutting unnecessary steps and maximizing efficiency.Improving Workflow Efficiency
Lean consultants design optimized workflows by restructuring production layouts, balancing workloads, and implementing just-in-time production, reducing lead times and enhancing throughput.Implementing Continuous Improvement Culture
They help embed a culture of continuous improvement through tools like Kaizen and 5S, ensuring long-term efficiency gains and empowering employees to drive future improvements.Tips on How to Hire Lean Operations Consultants
Selecting the right Lean Operations Consultant is essential for achieving significant, lasting operational improvements. Hereβs what to look for when hiring through Consultport:
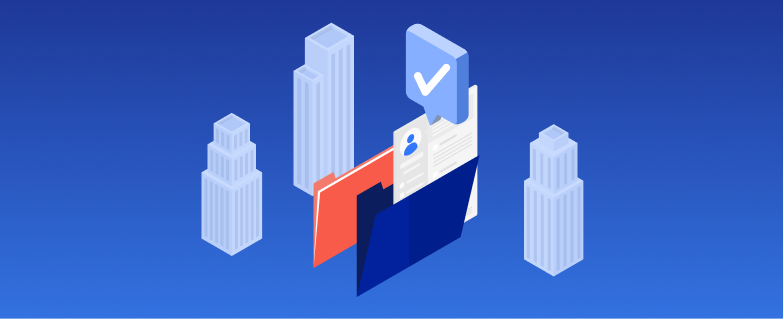
8+ Years of Experience in Operational Excellence or Manufacturing Firms
Your consultant should have at least a strong experience with leading lean transformation projects in leading manufacturing companies or top-tier consulting firms. This ensures they can navigate complex operational challenges and deliver tangible results.Lean Six Sigma Black Belt Certification
Look for certifications such as Lean Six Sigma Black Belt or Certified Lean Expert. These qualifications demonstrate that the consultant has mastered the methodologies necessary to drive efficient operations and process improvements.Industry-Specific Expertise:
Operational challenges differ across sectors. Hiring a consultant with deep expertise in your specific industryβwhether itβs automotive, pharmaceuticals, or logisticsβensures a tailored approach that meets your unique operational needs. They should be familiar with the operational demands and regulatory constraints of your industry.Trending Articles
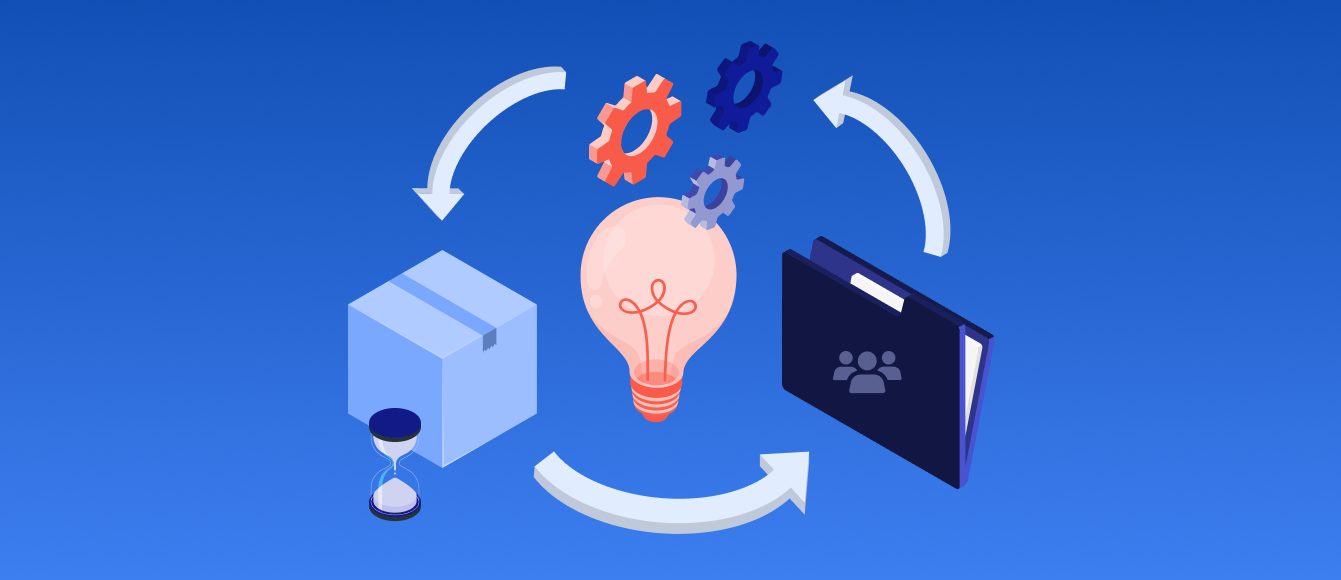
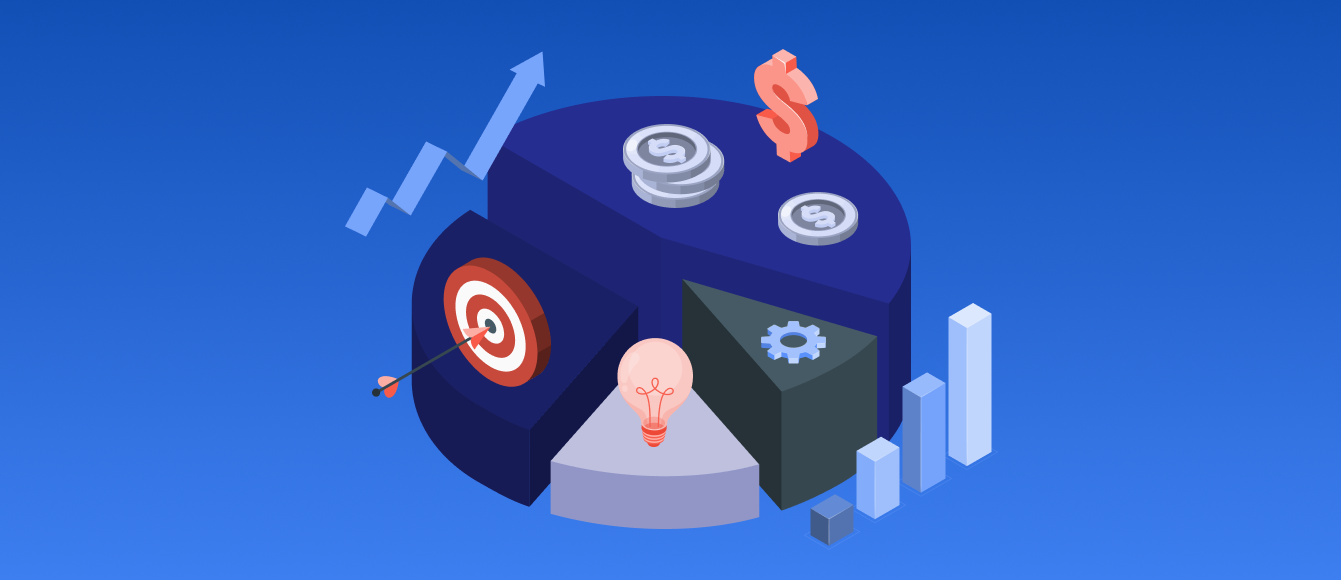
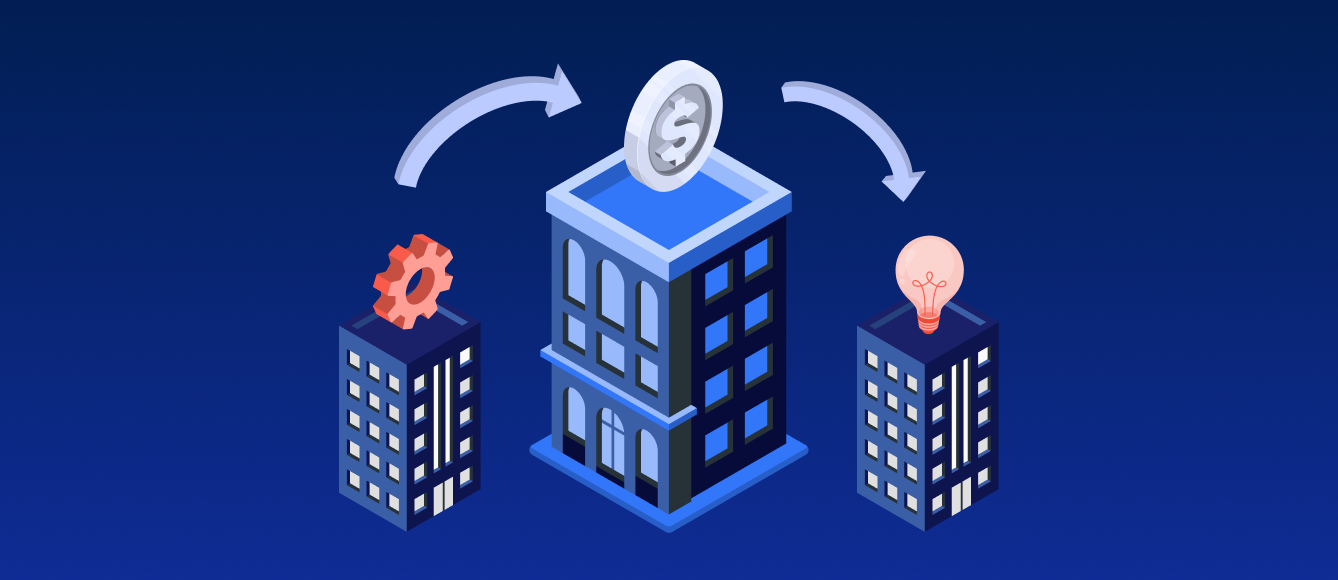