Unlocking Industry 4.0 with a Manufacturing Consultant
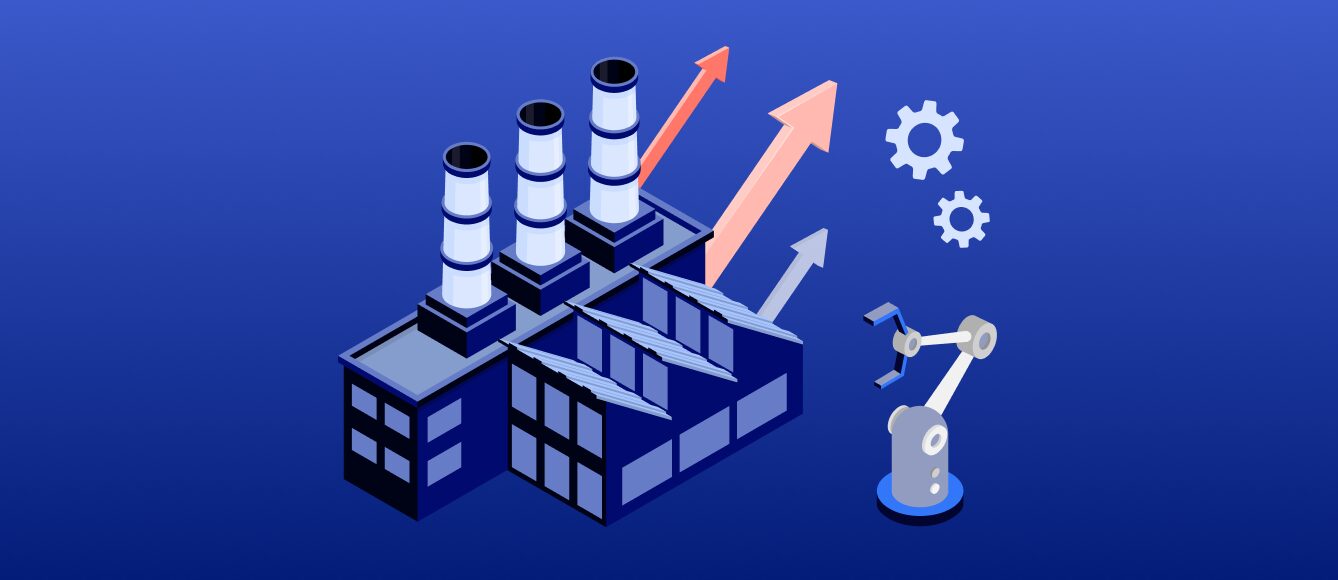
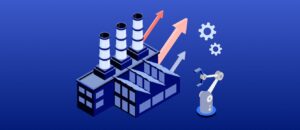
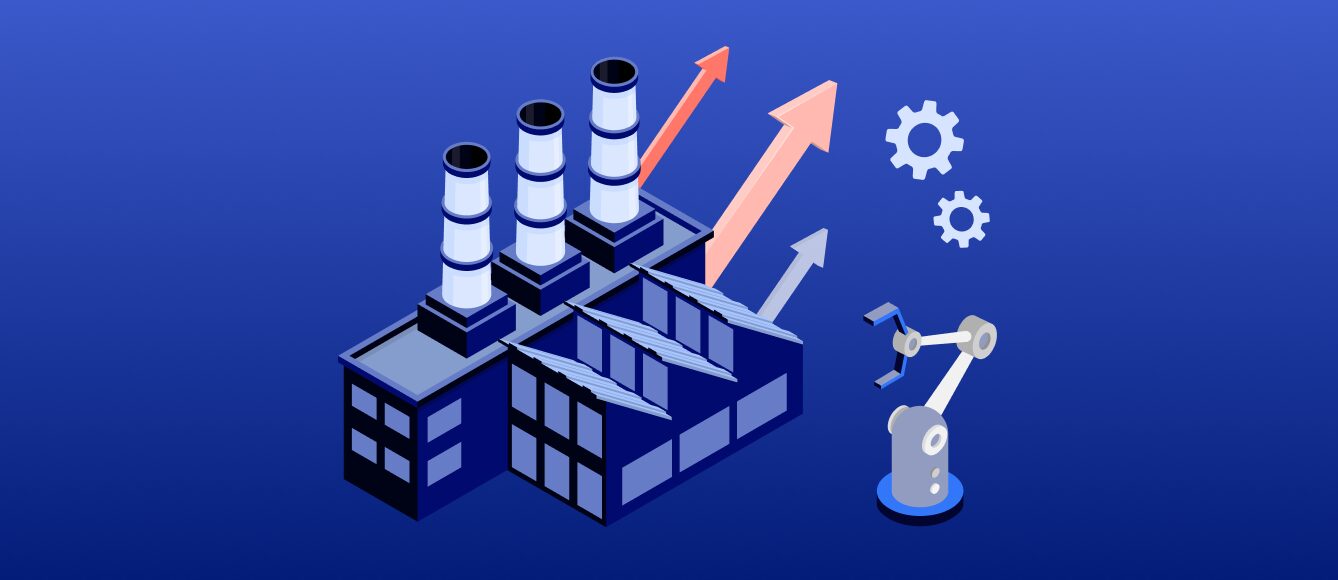
A manufacturing consultant assists manufacturing organizations or functions in optimizing their operations, integrating industry 4.0 technologies, and enhancing efficiency. As demand grows for digital transformation and automation, the manufacturing consulting market is set to expand rapidly.
However, the manufacturing industry is often facing significant challenges in the implementation of digital innovations. These include the lack of resources to scale complex technologies, overcoming talent shortages in specialized skills, and aligning existing workflows with advanced digital solutions. Nearly 50% of manufacturing professionals cite talent gap as a primary barrier to innovation, rather than technology.
This is where manufacturing consultants help. They bring expertise in critical areas such as Robotic Process Automation (RPA), Asset Optimization, and Workflow Automation. In this article, we will explore the role of manufacturing consultants, addressing the following key questions:
- What are the main challenges in implementing Industry 4.0 in manufacturing?
- How can a manufacturing consultant bridge the talent gap and support Industry 4.0 initiatives?
- What are the areas of expertise offered by OEE Optimization, RPA, Asset Optimization, and Workflow Automation consultants?
- How does a case study illustrate the value of a manufacturing consultant in overcoming Industry 4.0 challenges?
Industry 4.0 Demands Integrated Data Platforms in Manufacturing Departments
Industry 4.0 technologies have opened up new opportunities for speed, cohesion, flexibility, and automation, reshaping the manufacturing landscape. However, enabling Industry 4.0 within manufacturing requires a transformation of IT systems legacy, which can trigger significant challenges due to their monolithic structures.
Historically, manufacturing systems have been vertically integrated, with standalone applications like ERP and MES sitting on top of rigid control architectures. This structure, often compounded by proprietary protocols, limits agility and makes it difficult to respond to shifting market demands or operational needs quickly.
As manufacturing departments aim to transition to Industry 4.0, they face pressure to incorporate advanced technologies such as IoT, cloud computing, and machine learning. However, these technologies demand a shift from isolated IT and operational technology (OT) layers to a more interconnected, hybrid network.
As noted by BCG, this hybrid approach enables real-time data exchange across the production floor and IT systems, thus supporting predictive maintenance, quality control, and adaptive manufacturing processes.
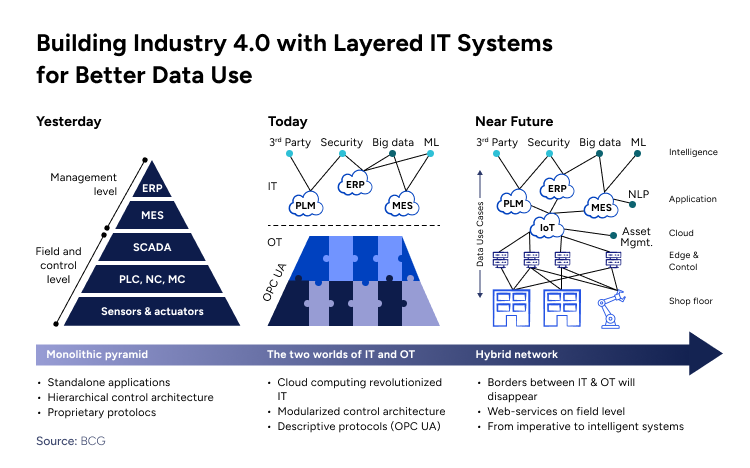
To overcome the constraints of legacy systems, manufacturing companies are embracing modular and cloud-based architectures. By adopting a modular approach, they gain flexibility, allowing for smoother upgrades, faster implementation of new technologies, and scalability across sites. Cloud computing and edge solutions enable data to be processed closer to the source, which minimizes latency and supports faster decision-making.
Despite Benefits, Companies Still Face Several Implementation Challenges
This shift to a hybrid IT-OT model facilitates data consolidation, essential for advanced analytics and machine learning applications. The impact of Industry 4.0 could lead to up to a 70% reduction in production defects, a 25% boost in productivity, and a 50% decrease in time-to-market.
However, scaling Industry 4.0 in manufacturing presents several key challenges that prevent companies from capturing value. According to McKinsey, only about 30% of companies fully benefit from Industry 4.0 investments, while the rest remain in the βpilot purgatoryβ phase due to significant barriers.
The most cited challenges are the following: resource limitations, unclear business value, high scaling costs, and an overwhelming number of potential use cases complicating prioritization.
- Resource and Knowledge Constraints: Many companies face a lack of skilled workforce and resources to scale Industry 4.0 initiatives effectively. Integrating new technologies requires a trained staff, which is often insufficient due to skill gaps in areas like data analytics and IoT infrastructure. Without the right skills, companies struggle to implement advanced tools or leverage the full benefits of automation.
- High Cost of Scaling: Companies might hesitate to invest heavily in manufacturing IT infrastructure and IoT connectivity due to the high initial costs. Large-scale investments, especially for cloud integration and real-time data processing, deter companies from moving beyond pilot projects. Cost-effective scaling, such as site-by-site rollout, can help mitigate this challenge.
- Business Case Justification: Industry 4.0 projects often require long-term investments, making it hard to justify based on short-term returns. Many firms seek immediate impact but find it challenging to measure ROI early on, especially for high-impact cases. This is where Minimum Viable Product (MVP) approaches can be beneficial by demonstrating economic potential through smaller, impact-focused implementations.
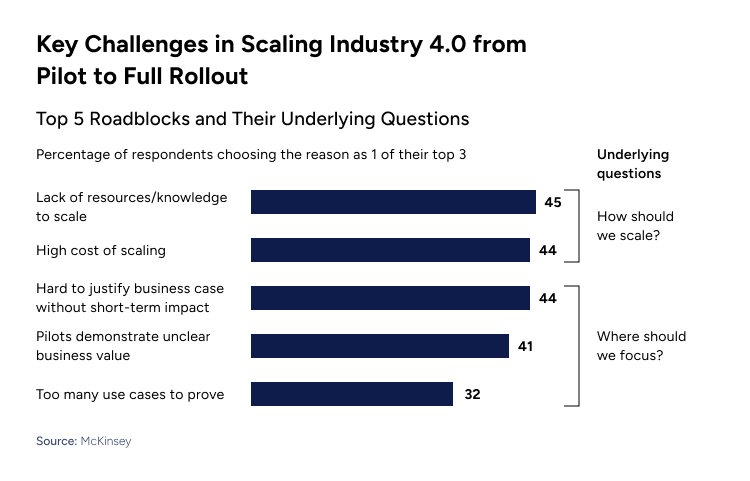
Where a Manufacturing Consultant Can Help
To enable Industry 4.0 transformation, a manufacturing consultant helps optimize production processes, manage quality control, and maintain compliance with environmental standards. Manufacturing consultants can also support throughout the innovation journey, pinpointing inefficiencies and implementing cost-effective scaling solutions for the newly established technologies.
Consulting platforms offer access to independent manufacturing consultants who bring deep expertise with a more flexible and cost-effective solution compared to traditional consultancies. Consultport offers access to qualified OEE Consultants, RPA Consultants, and Workflow Automation Consultants.
Overall Equipment Effectiveness (OEE) Consultants
Overall Equipment Effectiveness (OEE) Consultants are experts in enhancing machinery productivity by identifying and mitigating causes of inefficiency in key areasβavailability, performance, and quality. Their expertise is particularly valuable for capital-intensive manufacturing environments, where machinery utilization can impact the entire production chain.
In Industry 4.0, OEE optimization has shifted from traditional methods to data-driven analytics to identify the root causes of OEE loss. By collecting and analyzing granular production data, OEE consultants create transparency around machine operations and use this information to identify the exact sources of downtime, slowdowns, and quality defects.
- The process typically starts with establishing detailed OEE tracking, using digital tools for real-time event logging and time series data, such as changeover times, unplanned stoppages, and performance deviations.
- OEE consultants integrate these data points with higher-level informationβsuch as supply chain and maintenance schedules, shift data, and operator skill levelsβto conduct a comprehensive root cause analysis.
- Advanced analytics, including correlation analysis, reveal patterns of inefficiency that traditional methods might overlook.
- Benchmarking OEE performance across shifts, sites, and similar operations provides further insights, allowing manufacturing functions to prioritize actions based on data-backed evidence.
By optimizing machine availability and reducing cycle times, OEE Consultants help lower production costs and increase overall output. Additionally, their recommendations on asset utilization can inform strategic equipment investments and replacement decisions, ensuring that new machinery aligns with productivity standards before acquisition.
Robotic Process Automation (RPA) Consultants
Robotic Process Automation (RPA) Consultants specialize in automating repetitive and time-consuming tasks within the manufacturing workflow, enhancing efficiency and productivity. In labor-intensive industries like automotive and high-variant manufacturing, RPA consultants identify key areas for automation, such as:
- Material Handling
- Quality Inspection
- Inventory Tracking
Through RPA, these tasks can be executed faster and with greater precision, reducing operational costs and enabling to shift human resources toward more complex, value-added activities. Automating these processes can cut production time by up to 20%, significantly enhancing throughput.
In modern manufacturing, RPA consultants leverage advancements in:
- Machine vision: Enabling robots to handle high-variant environments with minimal setup adjustments.
- Collaborative robotics: Robots equipped with virtual safety fences can work alongside human workers, performing tasks like in-line quality inspections and low-speed assembly.
- Autonomous Guided Vehicles (AGVs): Extending automation by replenishing assembly lines and delivering parts in real time.
Moreover, RPA Consultants provide training to existing employees, equipping them with the skills needed to manage, monitor, and troubleshoot robotic systems. This training empowers the workforce to sustain automated processes independently, minimizing the need for constant external support and reducing the risk of workflow interruptions. RPA consultants design feedback loops that allow to continuously evaluate and optimize automated tasks, ensuring sustained efficiency improvements.
Workflow Automation Consultants
Workflow Automation Consultants specialize in designing and implementing automated workflows that bridge the gap between Information Technology (IT) and Operational Technology (OT), creating an integrated, hybrid network in manufacturing.
They streamline operations by eliminating manual tasks, reducing error rates, and enabling real-time data sharing between digital and physical systems. This hybrid approach is invaluable as it facilitates a seamless flow of data from the shop floor to higher-level management systems, enhancing both operational efficiency and strategic decision-making.
Key areas of workflow automation often include:
- Value-Stream Mapping: Consultants conduct a thorough analysis of existing workflows to identify inefficiencies and manual bottlenecks. By mapping out each step, they create a foundation for automating high-impact areas, ensuring that every task in the process is adding value.
- Digital Workflow Integration: By automating data collection and sharing across IT and OT, consultants enable systems such as ERP, MES, and IoT platforms to communicate effectively. This integration supports real-time monitoring and rapid responses to operational changes, reducing downtime and increasing productivity.
- Establish robust feedback mechanisms: RPA consultants also establish advanced feedback mechanisms to monitor the effectiveness of automated processes. They train existing staff on using and managing these integrated systems, ensuring that the organization can sustain automation efforts independently.
This continuous feedback and optimization process allows maintaining high efficiency and quickly adapt workflows. An integrated, hybrid IT-OT network, help operate in a more agile, data-driven environment, fostering long-term resilience and competitiveness in Industry 4.0.
Case Study: Manufacturing Consultant for Industry 4.0 Integration in Automotive Manufacturing
A German automotive parts manufacturer partnered with Consultport to create a digital roadmap for Industry 4.0, aiming to improve production efficiency, reduce downtime, and enhance overall equipment effectiveness (OEE). Consultport proposed three experienced consultants within 48 hours, and the company selected a manufacturing consultant with a track record in IoT, data analytics, and digital integration projects. The consultant focused on three key areas: IoT-enabled data collection, predictive maintenance, and IT-OT integration.
First, IoT sensors were installed on critical machinery to collect real-time data on machine status, cycle times, and energy use. This information was integrated into the companyβs ERP system, providing instant visibility across the production floor and empowering data-driven decision-making. Next, the manufacturing consultant introduced predictive maintenance through machine learning, analyzing historical and real-time data to identify signs of potential failures before they occurred.
Lastly, IT-OT integration established a hybrid network, connecting operational and information systems to allow seamless data flow. This integration enabled real-time adjustments to production schedules based on current machine performance, fostering agility and responsiveness.
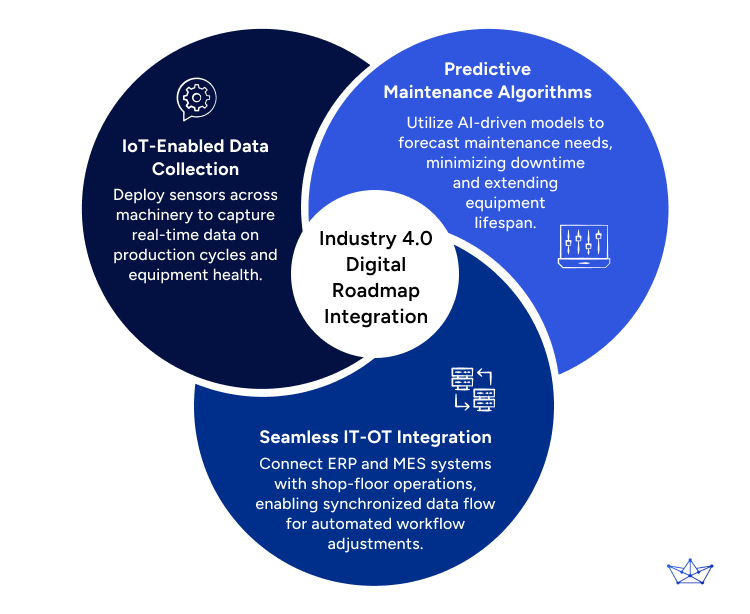
The 10-month project led to significant results: a 10% increase in OEE and reduction in maintenance costs, and a 15% decrease in energy consumption due to optimized machine use. Enhanced data transparency enabled faster decision-making, empowering the manufacturer to adapt operations swiftly.
By implementing this Industry 4.0 roadmap, the manufacturer built a robust digital infrastructure, significantly increasing efficiency and setting the stage for scalable, data-driven improvements in the future.
Want to know more? Find a Consultant with Consultport.
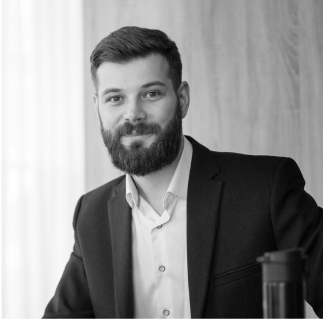
Daniel is a Process Excellence Consultant with several years of experience at McKinsey. He has specialized in enhancing efficiencies in the automotive and healthcare industries, working with prominent companies such as Ford, Daimler, and Pfizer. Daniel has experience in leading cross-functional teams and utilizing processes focusing on lean methodologies and continuous improvement to drive operational success.
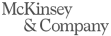
on a weekly basis.