How to Integrate Digital Lean Manufacturing and Agile
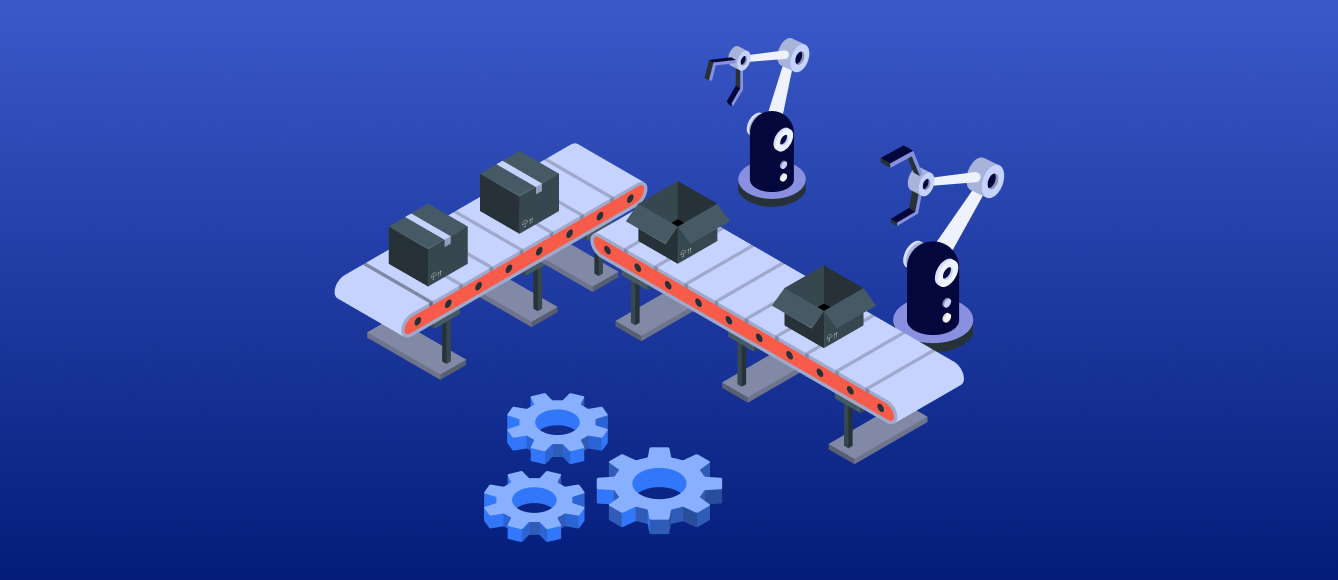
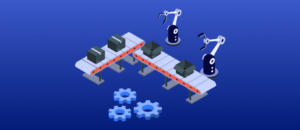
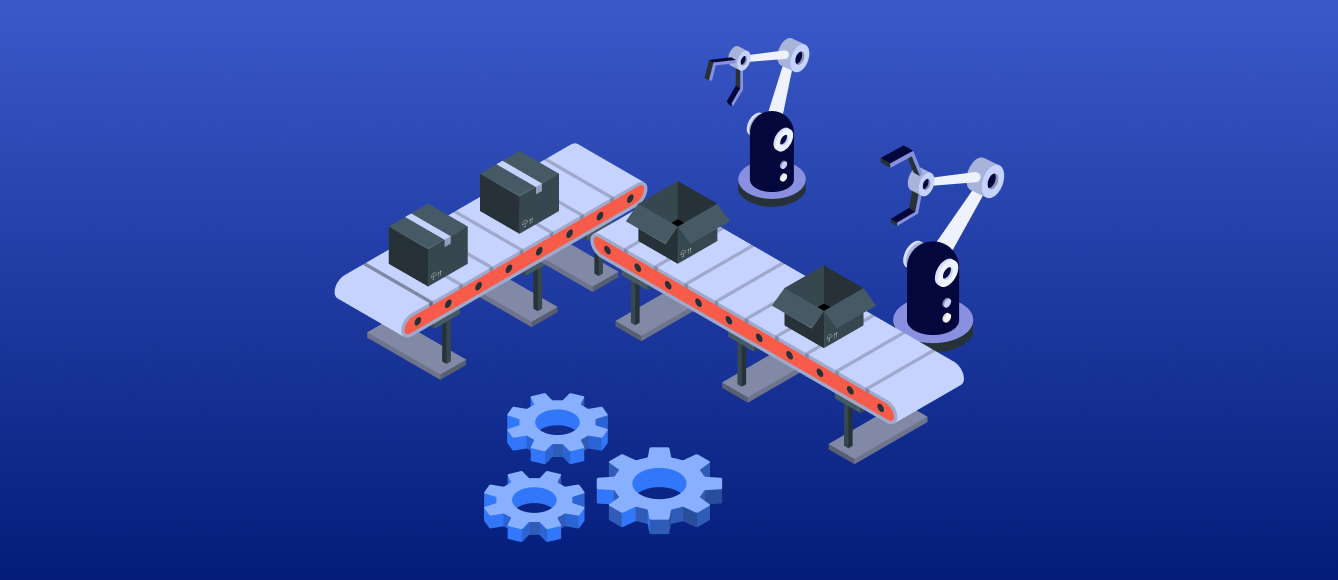
Lean manufacturing principles have been applied in manufacturing for decades, though the concept of reducing waste and improving efficiency existed long before the term "lean" became widely used. Over time, lean has evolved into a well-defined set of principles that have transformed the manufacturing industry. Nowadays, βDigital Leanβ refers to the integration of lean principles with digital technologies, especially automation and advanced analytics.
In recent years, Industry 4.0 technologies have introduced new possibilities for speed, cohesion, flexibility, and automation, reshaping the production landscape. Notably, innovations in robotics, materials, and artificial intelligence are set to play a leading role in the future of manufacturing.
Today, integrating digital technologies with lean principles is a concept known as "digital lean." This combination leverages the proven methods of lean with innovative digital tools to further reduce waste and variability in manufacturing processes, driving efficiency to new levels.
Moreover, when it comes to integrating lean manufacturing with agile methodologies, over 70% of companies fail to deliver the expected outcomes. Here is where Lean Manufacturing Consultants can provide critical support.
This article will explore how lean manufacturing is evolving in the digital age and, answering:
- What are the core principles of lean manufacturing?
- How does digitalization enhance traditional lean methods?
- What benefits does digital lean provide, and how can digital tools improve lean processes?
- How Lean Manufacturing Consultants can support organizations in this transformation?
What is Lean manufacturing?
Lean manufacturing, originating in the 1930s from Japan’s automotive industry, is a systematic approach focused on eliminating inefficiencies to optimize productivity and quality. One effective method to identify inefficiencies on the shop floor is through Gemba walks, which help teams observe processes firsthand and drive continuous improvement. For a structured approach, check out this guide on the Gemba Walk Checklist.
The core principle of lean is to maximize value by minimizing waste. This means that any activity or process that does add value to the customer must be reduced or removed.
The 5 Principles of Lean
The lean management system is built around five integrated disciplines that guide an organization’s strategy and operations.
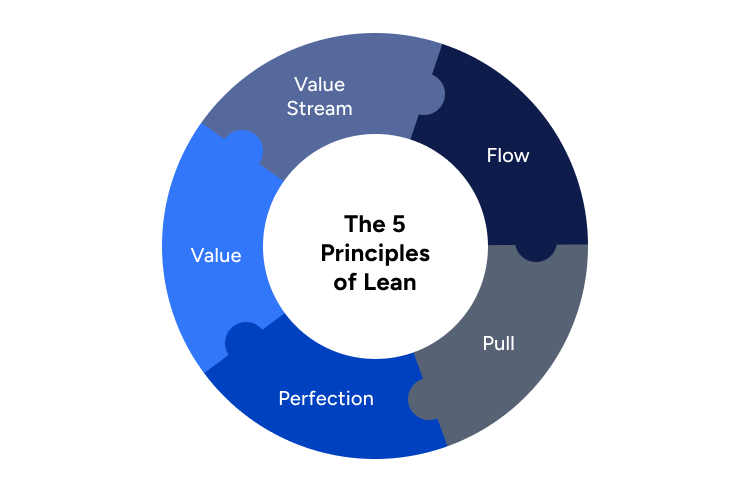
1. Value
Define the value that customers expect, and develop a strategy to align their expected value with product price. This can be done through interviews, surveys, demographic information, and web analytics. However, by using lean manufacturing principles the organization focuses only on the most relevant ones. This will reduce wasteful practices, while maintaining a competitive price.Β
Tools like Voice of the Customer (VOC) and Quality Function Deployment (QFD) help businesses translate customer expectations into technical specifications, allowing companies to reduce unnecessary features or production steps.
2. Value Stream
Identify and map the value stream for each product that delivers the expected customer value, and determine how to reduce or eliminate waste in each stage. The goal is to highlight areas of waste, inefficiency, or delay that do not add value to the customer.
A Value Stream Mapping (VSM) tool is key to visualizing the entire production process and identifying all actions required for the production. If any step in the value stream does not directly contribute to the end value perceived by the customer, it should be eliminated.
3. Flow
Create a method to maintain continuous flow throughout manufacturing and fulfillment processes, ensuring production is executed at the needed rates. Inspired by Toyota's Just-In-Time (JIT) system, the goal is to synchronize production with demand while minimizing delays and inventory waste.
Tools like Kanban are crucial to maintaining a smooth flow. Kanban manages work-in-progress and signals when replenishment is needed, while Takt Time aligns production pace with customer demand. Additionally, bottleneck analysis helps identify process stages where production flow is hindered, allowing teams to optimize throughput and reduce downtime.
4. Pull
Implement a pull system that triggers production only when there is demand, minimizing waste. This approach ensures that work is pulled based on real-time customer orders rather than speculative forecasting.
In a pull system, Demand Forecasting becomes a critical component, using ERP systems and machine learning algorithms to predict demand patterns and adjust production accordingly. This minimizes overproduction and the costs associated with excess inventory or warehousing, while also ensuring flexibility to adapt to changes in demand.
5. Perfection
Continuously analyze performance metrics to identify areas for improvement and enhance the customer experience. The focus is on refining every aspect of the production process—reducing the number of steps, time, and resources needed to deliver value. This involves setting up a tracking system and collecting data for each step, with the ultimate goal of removing inefficiencies, lowering costs, and focusing only on the steps that deliver value.
The 7 Kinds of Waste Addressed by Lean Manufacturing
By following these principles, lean manufacturing ensures that every process step is focused on value creation, cutting out unnecessary waste, and improving overall efficiency. In particular, Lean manufacturing addresses seven types of waste:
- Overproduction: Producing more than needed, leading to unused products.
- Inventory: Excess stock of raw materials or finished goods that tie up capital.
- Transport: Unnecessary movement of materials or products.
- Movement: Inefficient movements by workers or machinery that don’t add value.
- Overprocessing: Using more resources than required for a task.
- Defects: Errors that result in rework or discarded products.
Waiting: Delays in production due to downtime or bottlenecks.
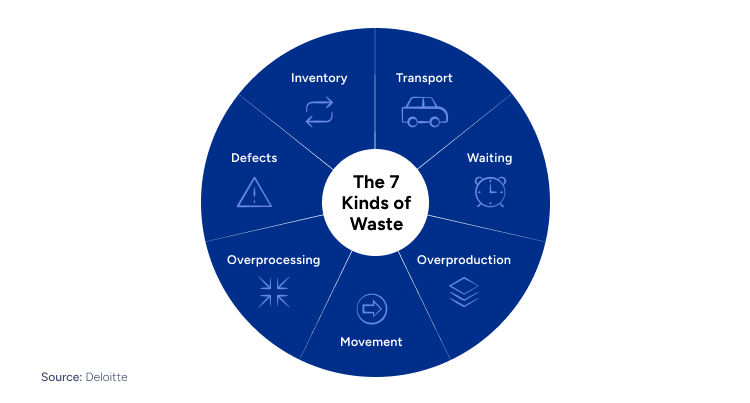
Digital Lean vs. Traditional Lean
Overcoming Traditional Lean's Limitations with Digital Lean and Industry 4.0
Overall, traditional lean manufacturing methodologies target specific types of waste and aim to improve overall processes by focusing only on value-added activities. However, it often faces limitations in addressing variability and real-time adjustments. Lean principles were initially designed for manual, human-driven systems, which can sometimes lack the speed and adaptability required in today's fast-changing market environment.
Digital lean, on the other hand, integrates advanced digital technologies (Industry 4.0) with traditional lean principles. Digital lean enhances visibility into operations, allowing companies to monitor and adjust production processes in real time.
Industry 4.0 significantly enhances factory value by embedding digital technologies into conventional processes. In fact, traditional lean embeds Six Sigma and labor arbitrage methodologies, but these methods provide incremental value until they encounter a complexity barrier, limiting further value creation.
Here is where Industry 4.0 helps: by introducing digital solutions such as quality sensing, factory asset intelligence, dynamic scheduling, and augmented workforce, the new value curve unlocks a significant upward potential, surpassing the traditional lean optimization approach. Digital lean systems provide detailed data on every aspect of the process, strengthening the application of lean principles and boosting the impact of tools like Kanban.
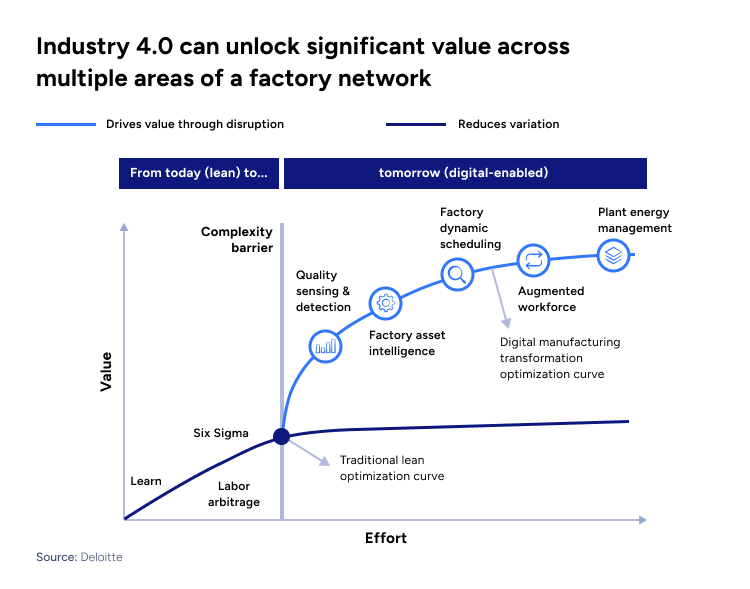
Lean Digital Tools to Improve Processes
To better understand their impact, let's consider three commonly used lean manufacturing methodologies: Kanban, Total Productive Maintenance (TPM), and Heijunka.
Kanban helps regulate inventory by signaling when resources need replenishment, while TPM ensures that machinery is maintained regularly to prevent breakdowns. Heijunka balances production workloads, ensuring smooth operations and avoiding bottlenecks.
With the rise of Industry 4.0, these tools are being enhanced by digital technologies. Kanban, for instance, benefits from RFID sensors and real-time data, which allow companies to automatically monitor inventory levels and replenish materials when required.
Predictive maintenance, a digital evolution of TPM, leverages IoT sensors and machine learning algorithms to anticipate equipment failures before they happen, reducing downtime and maintenance costs. Advanced analytics can further improve Heijunka by optimizing production schedules based on historical data and real-time conditions.
Additionally, digital tools like digital twins, augmented reality, and AI-powered simulations are transforming how manufacturers approach production. A digital twin creates a virtual replica of the production environment, enabling manufacturers to simulate different scenarios, optimize workflows, and prevent disruptions before they occur.
Automation technologies, such as guided vehicles and automated container handling, streamline labor-intensive processes, reducing manual intervention and speeding up production times. These digital tools work smoothly with lean methodologies to create a more data-driven production system that maximizes efficiency and minimizes waste.
The Benefits of Integrating Digital Tools in Lean Manufacturing
Implementing digital technologies in lean manufacturing can minimize overproduction thanks to:
- Accurate demand forecasting.
- Monitoring of inventory levels through sensors.
- Detection of defects in an early stage through machine learning algorithms.
Unlike traditional lean, which reacts to inefficiencies after they occur, digital lean enables proactive management of processes by providing continuous data insights and automated solutions.
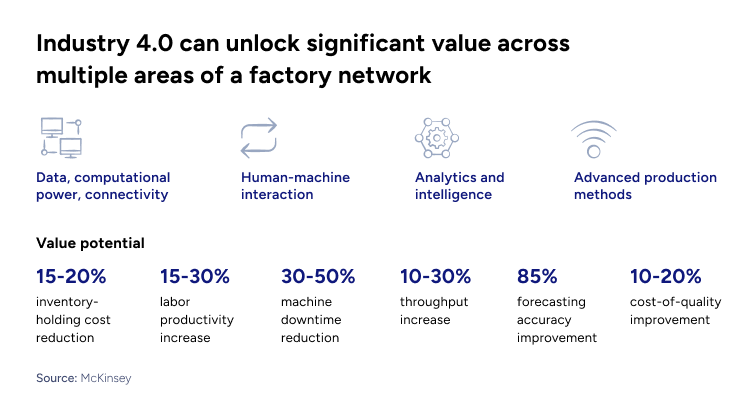
This evolution enhances traditional lean principles by utilizing real-time data, advanced analytics, and automation to optimize efficiency and reduce costs. For instance, Industry 4.0 can lead to a 15–20% reduction in inventory-holding costs, a 30–50% reduction in machine downtime, and a 15–30% increase in labor productivity.
Advanced analytics and AI also improve throughput by 10–30%, while forecasting accuracy increases by 85%, leading to better production planning and cost efficiency. Let’s explore more in detail how digital technologies and lean manufacturing can go hand-in-hand.
Combining Lean and Agile
When deciding between agile and lean, many leaders believe they must choose one approach over the other. However, this is a misunderstanding. Both methodologies share core objectives: delivering customer value efficiently, fostering continuous improvement, and empowering teams. Rather than viewing them as separate, combining agile and lean often yields better results.
As underlined in a recent Consultport Report on Agile Methodologies, agile has several benefits, including quality control, increased productivity, and reduced project risks. Agile emphasizes iterative development, where teams release early versions of products or services, gather customer feedback, and make improvements rapidly. It benefits quality control, increased productivity, and reduced project risks.
Lean, on the other hand, emphasizes practices like Kaizen and visual workflow management to optimize efficiency and eliminate waste. Both systems use tools like Kanban to manage workflows, with daily performance dialogues, value-stream mapping, and problem-solving techniques.
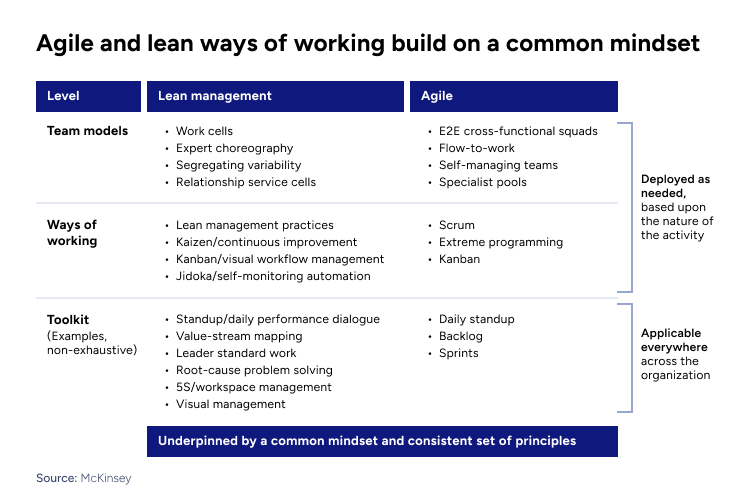
Lean excels in structured, repeatable processes, making it ideal for tasks like production operations with predictable demand. Agile suits environments that require adaptability and cross-functional collaboration.
Self-managed teams and relationship service cells offer flexibility, working for both predictable and creative, customer-facing tasks. On the other hand, agile models like cross-functional squads and flow-to-work pools are designed for more variable, creative tasks, including business partnering and engineering support. The choice of model depends on the nature of demand (predictable or variable) and the type of activity (routine or creative).
By combining lean and agile, companies can more comprehensively address diverse organizational needs, adapting their approach based on the nature of demand and type of activity. This integration ensures operational success by leveraging the strengths of both methodologies.
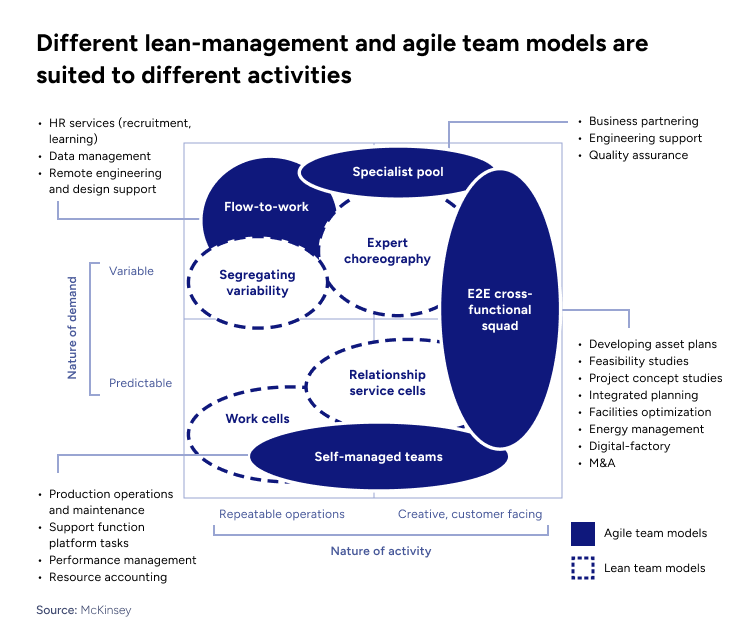
Lean Manufacturing Consultants: Drive Lean Transformation
Despite the wide popularity of this methodology, some empirical studies assess how failure rates for lean manufacturing and digital lean are between 60% and 90%, with around 30% delivering almost no business value.
That’s why Lean Manufacturing Consultants can add value. They help in identifying and minimizing waste in production, particularly in case of demand fluctuations or when new production lines are introduced. Most importantly, they provide expert guidance and leadership support, assessed as one of the most critical success factors.
What to Look for in Lean Manufacturing Consultants
When selecting a lean manufacturing consultant, several key factors should be considered to ensure you're partnering with the right expert. At Consultport, only the best-performing consultants are on the platform, with a stringent vetting process where only the top 2% of applicants are accepted.
Some criteria to consider when hiring a lean manufacturing consultant include:
- Years of Experience at Top-Tier Firms or Global Corporations: Look for consultants with at least 10 years of experience working for top-tier consulting firms or as senior lean managers at global manufacturers, depending on industry-specific qualifications. This level of experience ensures they have mastered lean principles and have applied them in complex, high-impact environments.
- Advanced Certifications in Lean and Six Sigma: The consultant should hold top certifications like Lean Six Sigma Black Belt or Master Black Belt from globally recognized institutions such as ASQ or IASSC. These certifications demonstrate mastery of advanced lean methodologies and the ability to execute large-scale transformation projects.
- Expertise in Industry 4.0 and Digital Tools: Top profiles have extensive experience integrating digital lean tools, such as IoT-based Kanban systems, ERP platforms, and real-time analytics. They should be able to leverage tools like predictive maintenance software, AI-driven process automation, and digital twins to enhance lean processes and improve operational efficiency in data-driven environments.
Case Study: Implementing Lean Manufacturing for Industrial Products Company
A leading industrial products manufacturer in the UK engaged Consultport to implement digital lean manufacturing practices across their production processes. The project aimed to streamline operations, reduce waste, and enhance productivity using advanced digital tools.
Consultport proposed three highly qualified consultants within 48 hours, and the company ultimately chose a senior consultant with 13 years of experience in digital lean transformation for industrial manufacturing.
To achieve the client’s objectives, the consultant focused on two key areas: real-time data integration and predictive analytics.
First, they implemented IoT sensors across the production floor to monitor machinery, inventory levels, and production cycles in real time. This data was centralized in an ERP system, allowing instant visibility into key performance metrics. The consultant also developed digital Kanban systems to optimize workflow and inventory management, ensuring the right materials were available just in time for production.
Next, the consultant integrated predictive maintenance algorithms using machine learning to detect potential equipment failures before they occurred. This allowed the client to reduce downtime significantly. Furthermore, by using AI-driven simulations, they were able to analyze production bottlenecks and test different process adjustments virtually, ensuring optimal production flow without disrupting ongoing operations.
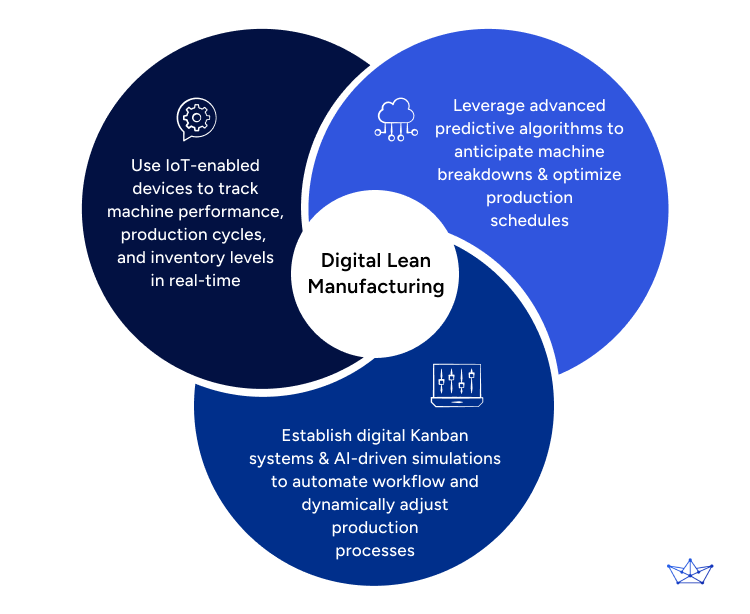
The results of the 12-month project were substantial. The client saw a 25% reduction in downtime, a 15% increase in overall equipment efficiency (OEE), and a 30% reduction in inventory holding costs. Additionally, through continuous monitoring and predictive analytics, the client experienced a 20% reduction in maintenance costs, improving overall profitability. By integrating digital lean practices, the manufacturer enhanced their operational efficiency and positioned themselves to better meet future production demands.
Want to discover more? Find a Consultant
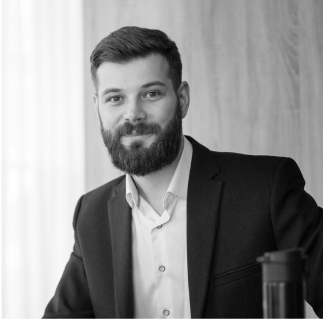
Daniel is a Process Excellence Consultant with several years of experience at McKinsey. He has specialized in enhancing efficiencies in the automotive and healthcare industries, working with prominent companies such as Ford, Daimler, and Pfizer. Daniel has experience in leading cross-functional teams and utilizing processes focusing on lean methodologies and continuous improvement to drive operational success.
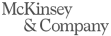
on a weekly basis.