Case Study | Lean Management Optimization for Maritime Logistics
Functional Topic
Lean Process Optimization
Project Industry
Logistics & Transportation (Maritime)
Needed Support
1 Lean Manufacturing Consultant
Duration
3 Months
The Challenge
A boutique consulting company engaged Consultport to find an expert in lean management and continuous process optimization to improve the monthly forecasting process of one of their clients, operating in the maritime logistics industry.
The client aimed to streamline vessel forecasting (in planning or production), focusing on reducing resource consumption and improving efficiency in controlling and planning processes. This project required an experienced consultant skilled in lean optimization with a particular focus on the maritime sector.
Role of Consultport
Consultport responded quickly, providing within 48 hours a shortlist of qualified consultants with lean optimization expertise. The client selected a Lean Manufacturing Consultant with extensive experience in process optimization, specialized in the logistics and transportation industries. The consultantβs primary objective was to refine the forecasting process, minimize waste, and streamline operations to improve forecasting accuracy and resource management.
The Approach
The consultant applied a structured lean and Six Sigma approach to optimize the clientβs forecasting and resource management processes, and to drive efficiency and accuracy in forecasting.
1. Diagnostic and Process Mapping
The project began with Value Stream Mapping (VSM) and stakeholder interviews to identify bottlenecks and inefficiencies in the forecasting and controlling processes. This assessment provided a clear view of where delays and redundancies occurred, guiding the optimization strategy.
2. Lean Process Optimization and 5S Implementation
By implementing 5S principles (Sort, Set in order, Shine, Standardize, Sustain), the consultant organized data handling processes to improve speed and reduce errors. Workflows between planning and production were restructured to enable smoother transitions and reduce lead times.
3. Six Sigma DMAIC Framework
Using the DMAIC (Define, Measure, Analyze, Improve, Control) framework, the consultant focused on reducing forecasting errors. They redesigned data protocols, introduced statistical models, and established KPIs to monitor forecast accuracy and resource use in real time.
4. Predictive Analytics and IoT Integration
Predictive analytics and IoT sensors were introduced to monitor equipment and adjust schedules based on real-time and historical data. This integration allowed the company to respond proactively to demand changes and minimize downtime.
5. Continuous Improvement through KaizenΒ
The consultant facilitated Kaizen workshops, fostering a culture of continuous improvement. These sessions empowered employees to identify and implement incremental changes, ensuring sustained efficiency gains.
The Results
At the end of the project, the client observed significant improvements in forecast accuracy and resource management:At the end of the initial phase, the client observed significant improvements in forecast accuracy and resource management:
20% Improvement in Forecasting Accuracy
With a more precise forecasting process, the client minimized discrepancies and improved planning effectiveness.
Reduction in Resource Wastage
Lean management practices reduced unnecessary resource consumption, aligning usage with actual demand.
Enhanced Efficiency in Planning and Production
The optimized process provided better control over planning and production, improving responsiveness and resource allocation.
Boosted Operational Sustainability
The consultantβs expertise in lean optimization empowered the maritime company to operate with enhanced efficiency and reduced waste.

The consultant helped us drive this project without the need for a new hire. We’re very happy with the results achieved, and we look forward to working with them again.
β Partner, Consulting Firm
Trending Articles
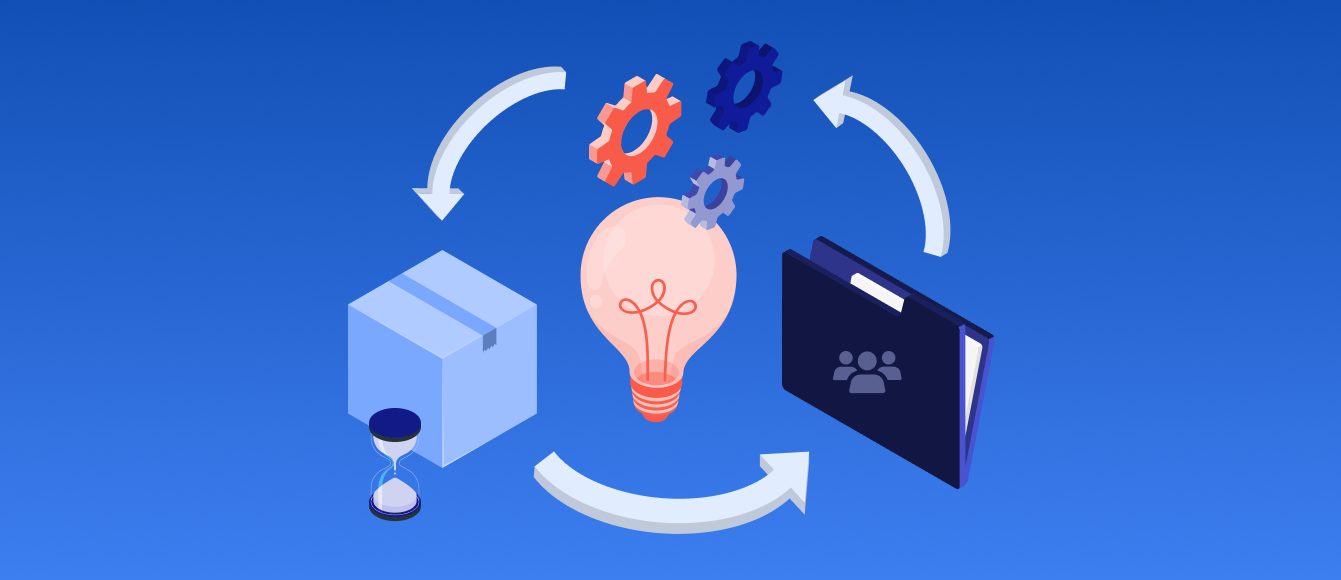
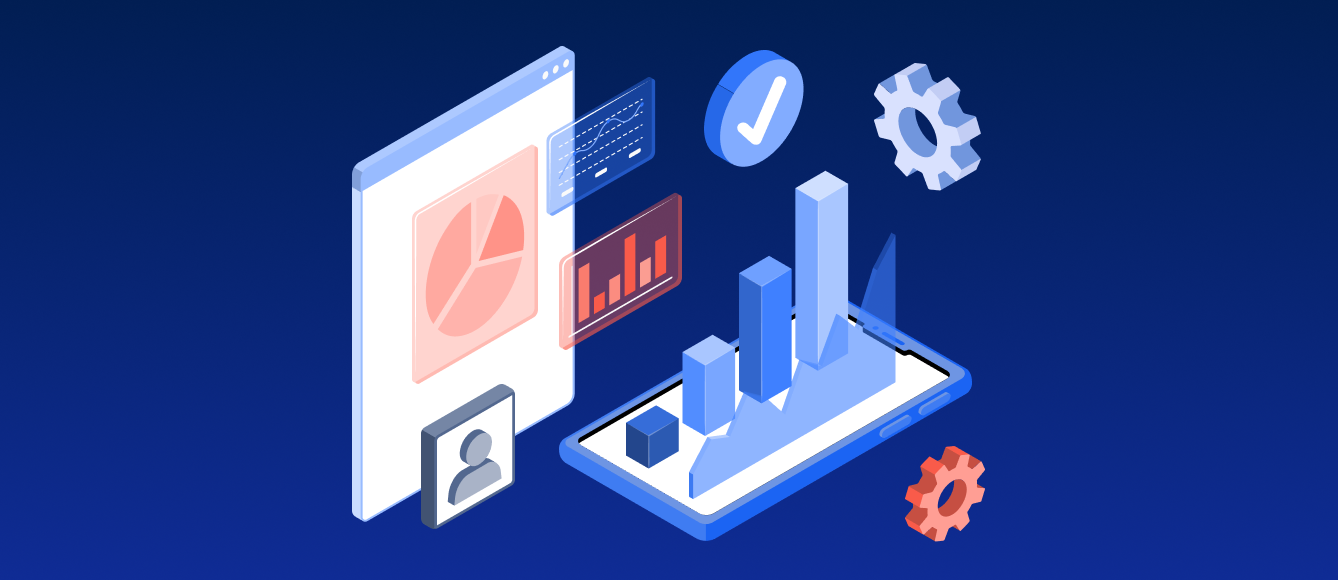
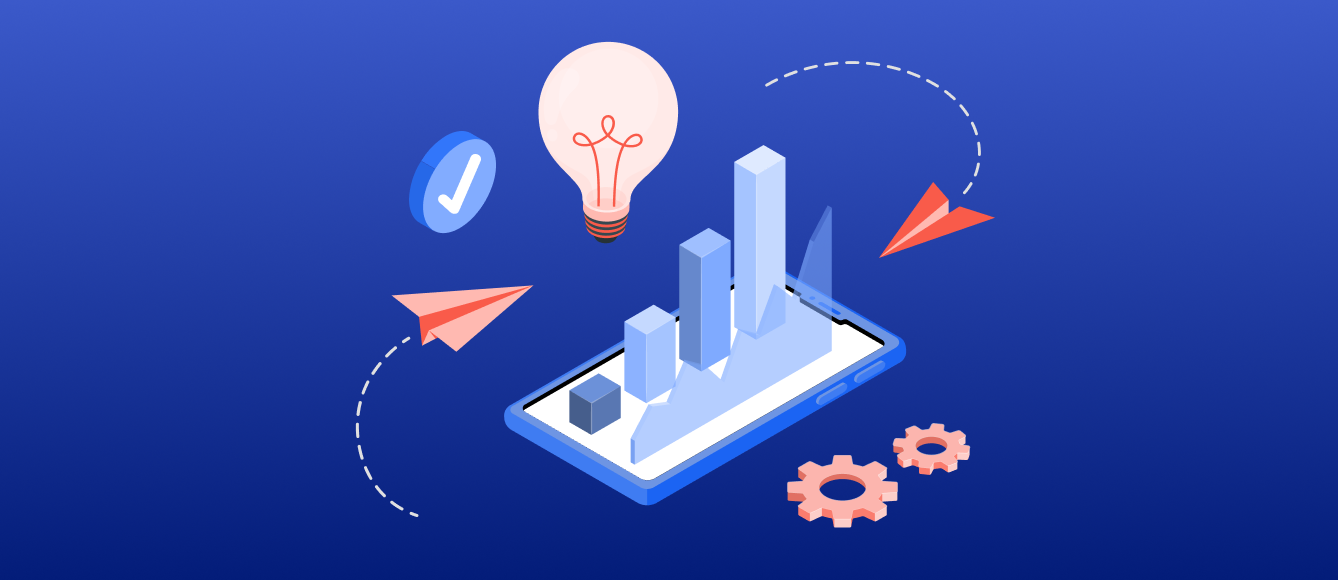
"*" indicates required fields