Case Study | AI Integration in Smart Manufacturing for a Global Electronics Manufacturer
Functional Topic
AI in Smart Manufacturing
Project Industry
Electronics Manufacturing
Needed Support
Artificial Intelligence Consultant
Duration
6 Months
The Challenge
A global electronics manufacturer aimed to modernize its production facilities by adopting smart manufacturing practices. Although the company had already invested in IoT devices and robotics, the lack of AI integration limited their potential. Operational inefficiencies, such as unplanned machine downtime, disrupted workflows, and siloed data systems, created significant challenges.
The company needed to leverage AI in smart manufacturing to centralize data, predict and prevent equipment failures, and optimize production processes. Moreover, they sought a solution that could be scaled across multiple facilities, ensuring consistent improvements in operational efficiency and output quality.
Role of Consultport
To address these challenges, the company engaged Consultport to identify a highly qualified Artificial Intelligence consultant specializing in smart manufacturing transformations. Within 48 hours, Consultport proposed three consultants, each with extensive experience in AI implementation within the manufacturing sector.
The selected consultant had managed 6 previous projects in applying AI in industrial environments, with expertise in predictive analytics, process optimization, and scaling AI systems across multiple sites. This combination of skills and experience made them uniquely suited to drive the companyβs implementation of AI in smart manufacturing and transition to a smart factory model.
The Approach
The consultant employed a structured methodology to achieve a complete AI integration in smart manufacturing:
Data Integration and Predictive Maintenance
To address the issue of data silos, the consultant centralized machine and sensor data into a unified data lake using Snowflake. This process involved consolidating inputs from IoT sensors, programmable logic controllers (PLCs), and enterprise resource planning (ERP) systems. Moreover, the consultant designed machine learning models using Python and TensorFlow, focusing on predicting equipment failures. By training these models on five years of historical machine data and integrating real-time IoT sensor inputs, the company could anticipate potential issues before they occurred.
Automation and Process Optimization
AI in smart manufacturing was further utilized to automate production workflows and optimize scheduling. The consultant integrated AI-driven process management tools into the companyβs existing manufacturing execution systems (MES). This optimization enhanced production line efficiency, minimizing delays and enabling more agile operations.
Creating a Scalable AI Framework, Conducted Workforce Training
The consultant developed a scalable AI smart manufacturing architecture using Kubernetes, allowing the company to deploy AI models across 12 global production sites. This approach reduced the rollout time for new facilities from six months to just four weeks. Moreover, the consultant conducted intensive training programs for over 50 plant managers and engineers. These workshops covered the practical use of AI in smart manufacturing, including how to interpret analytics, maintain predictive models, and adapt workflows to AI-driven insights.
The Results
The integration of AI in smart manufacturing yielded significant, measurable outcomes for the company:
Increased Operational Efficiency
Thanks to the data centralization and automation of workflows, productivity rose significantly, streamlining operations and increasing operational efficiency.
Cost Reduction
Predictive maintenance efforts reduced unplanned downtime, allowing significant savings in maintenance costs, also extending the lifespan of manufacturing equipment.
Increased Scalability
AI models were successfully deployed across all 12 global facilities, reducing the cost and complexity of scaling the smart manufacturing ecosystem.
Workforce Training
The training programs ensured that plant managers and engineers could independently manage AI systems, fostering a culture of continuous improvement within the organization.

The team brought immense value by showing us what to focus on for future growth.
β Director of Business Development
Trending Articles
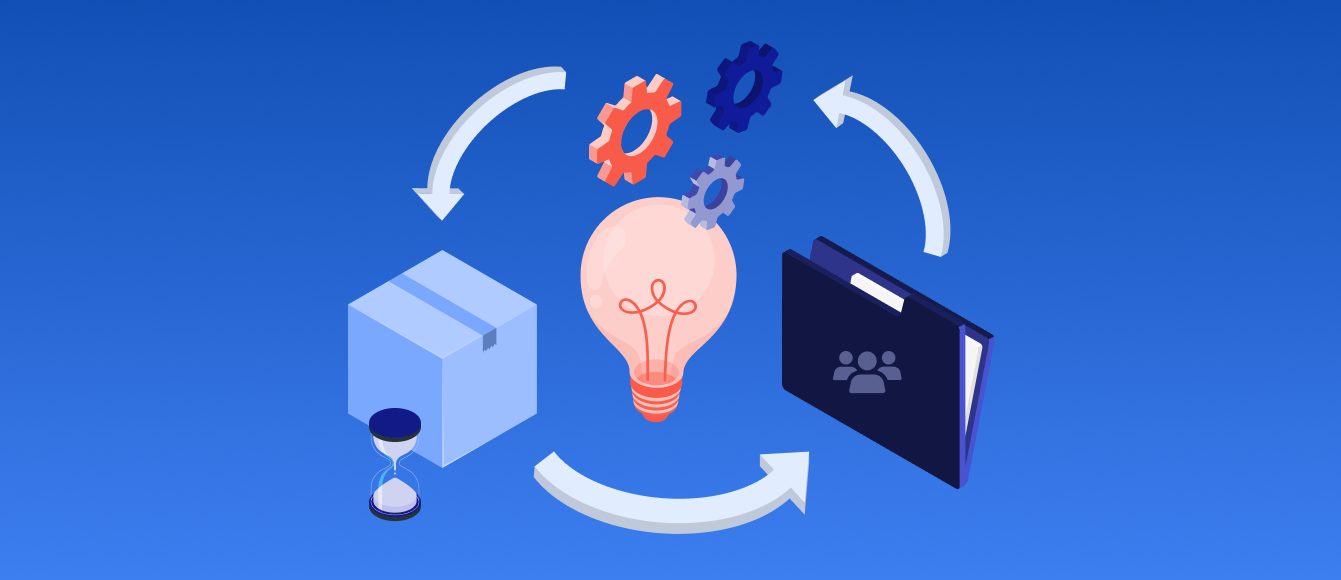
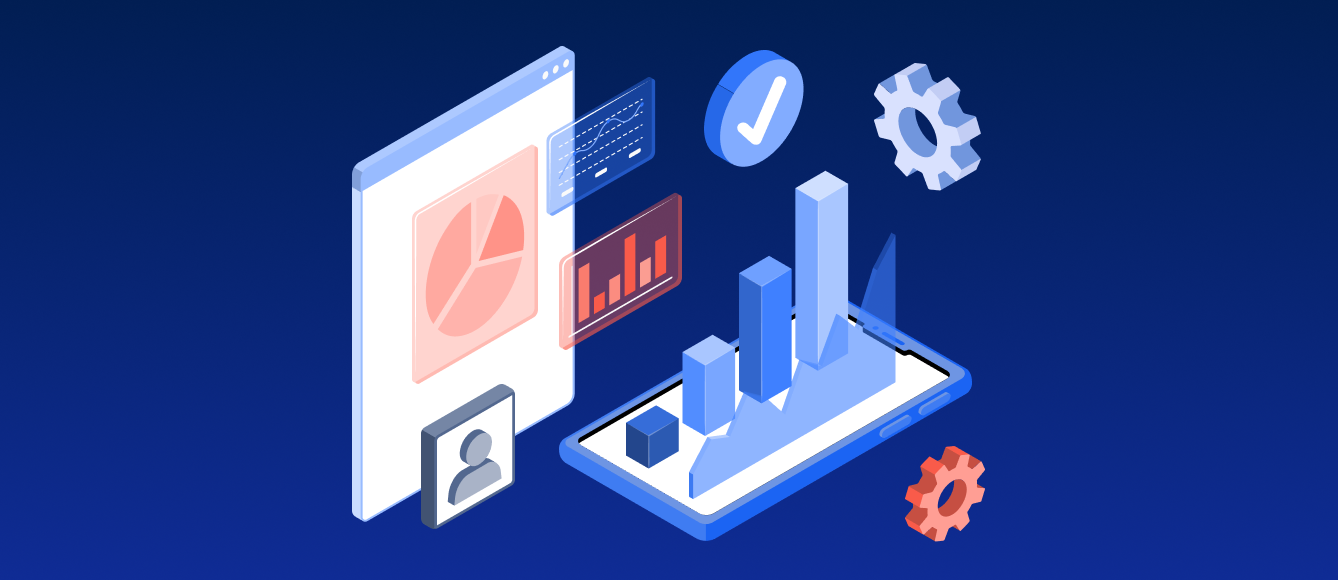
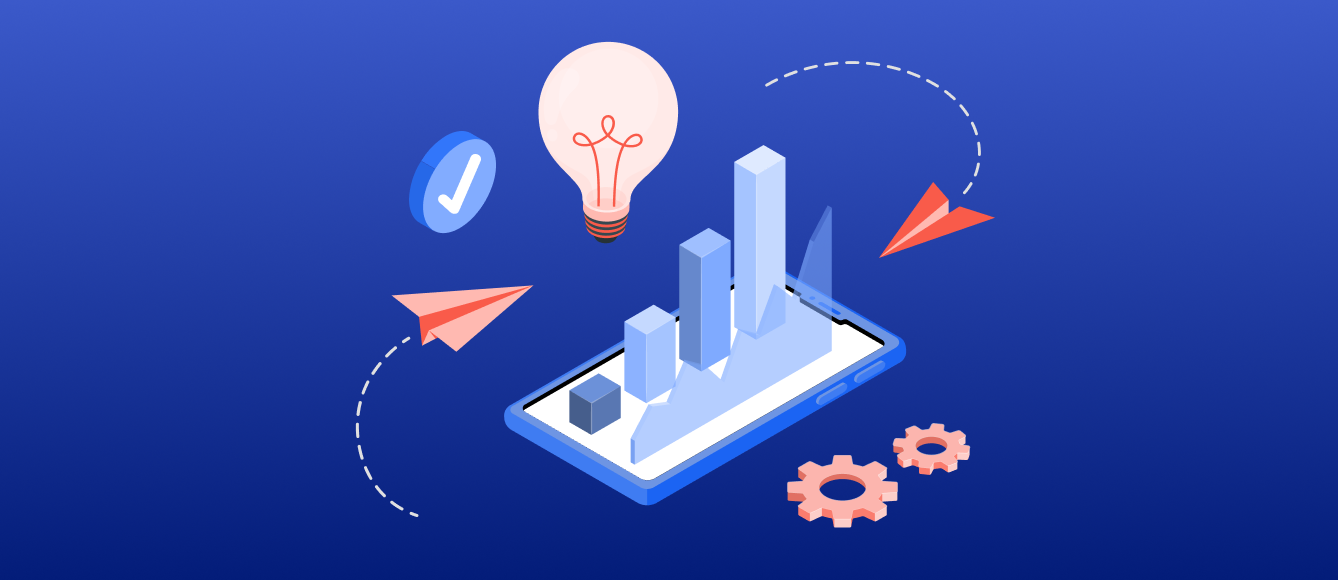
"*" indicates required fields