Case Study | Digital Lean Manufacturing for Industrial Products Company
Functional Topic
Digital Lean Manufacturing Transformation
Project Industry
Industrial Products
Needed Support
1 Manufacturing Consultant
Duration
3 Months
The Challenge
A leading industrial products manufacturer in the UK engaged Consultport to implement digital lean manufacturing practices across their production processes. The client sought to streamline operations, reduce waste, and enhance productivity through advanced digital tools, aiming for a comprehensive transformation to improve overall efficiency. They required an expert consultant with extensive digital lean transformation experience to successfully guide the project.
Role of Consultport
Consultport responded quickly, presenting a shortlist of three highly qualified consultants within 48 hours. The manufacturer chose aΒ Manufacturing Consultant with over 7 years of experience in lean transformation specifically tailored for industrial manufacturing. The consultant’s role was to design and implement a lean manufacturing strategy integrating real-time data and predictive analytics, ensuring optimized and waste-reduced production processes.
The Approach
The consultantβs approach focused on integrating real-time data and predictive analytics to drive the digital lean transformation:
- Real-Time Monitoring: They began by implementing IoT sensors across the production floor to track machinery, inventory levels, and production cycles in real time. This data was centralized within an ERP system, giving the client immediate visibility into key performance metrics and enabling quick adjustments to boost efficiency.
- Workflow and Inventory Optimization: The consultant developed digital Kanban systems to optimize workflow and manage inventory, ensuring that materials were available βjust in timeβ for production.
- Predictive Maintenance: To further enhance operations, predictive maintenance algorithms were integrated using machine learning to detect potential equipment failures before they occurred, significantly reducing downtime.
- AI-Driven Simulations: By employing AI-driven simulations, the team could analyze production bottlenecks and test process adjustments virtually, ensuring an optimal production flow without disrupting ongoing operations.
The Results
After one year of the projectβs conclusion, the client reported substantial improvements in their manufacturing activities to better meet production demands and improve profitability.
25% Reduction in Downtime
By implementing predictive maintenance and real-time monitoring, the client minimized unplanned downtime, boosting operational continuity.
15% Increase in Overall Equipment Efficiency (OEE)
Enhanced workflow management and lean practices improved equipment utilization, leading to a marked increase in efficiency.
30% Reduction in Inventory Holding Costs
The digital Kanban system optimized inventory management, resulting in significant cost savings by minimizing unnecessary stock.
20% Reduction in Maintenance Costs
Predictive analytics helped prevent costly repairs and extended equipment lifespan, reducing overall maintenance expenses.

The consultant helped us realize a significant transformation. Weβre now operating more efficiently and are well-prepared for future demands. We look forward to working with them again.
β Director of Business Development
Trending Articles
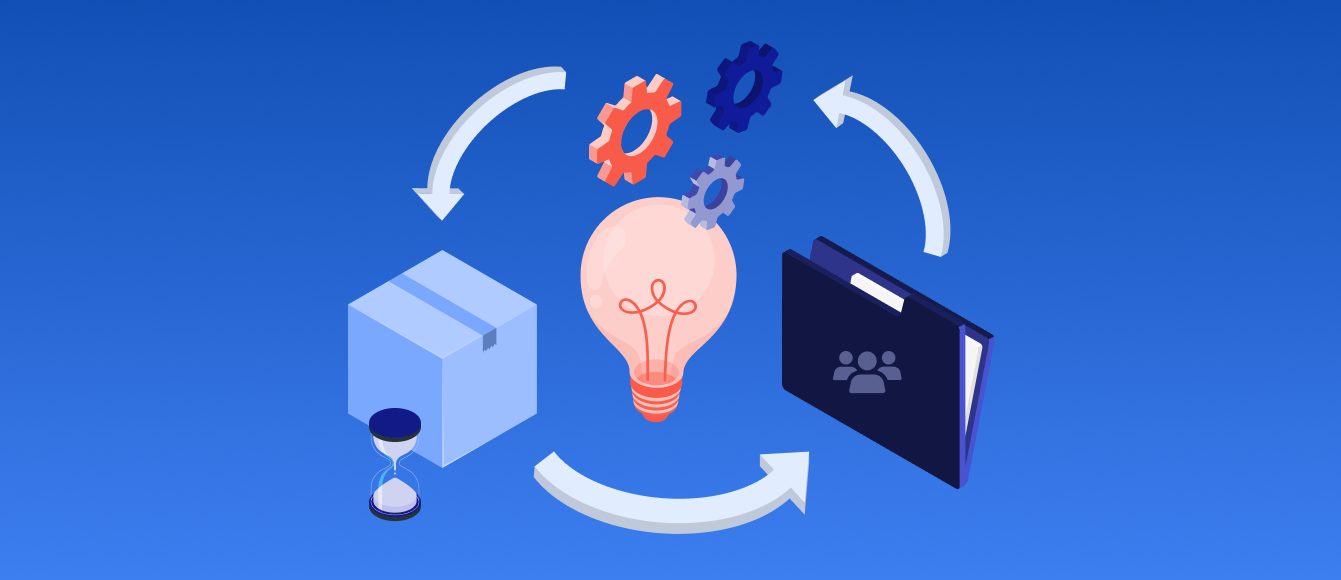
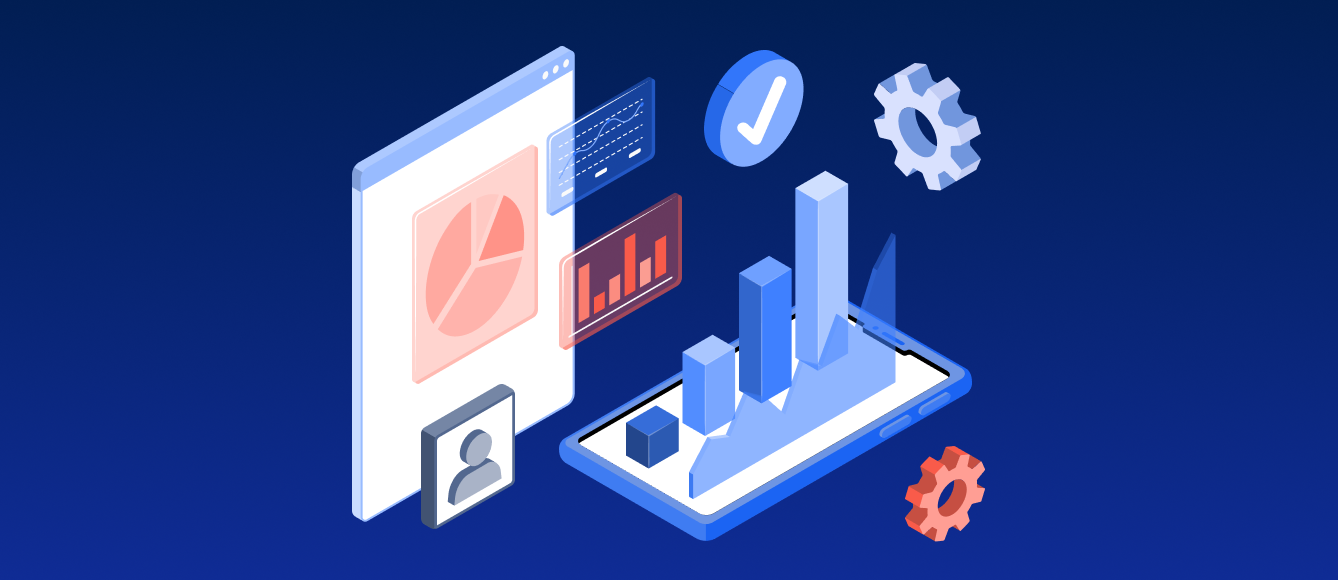
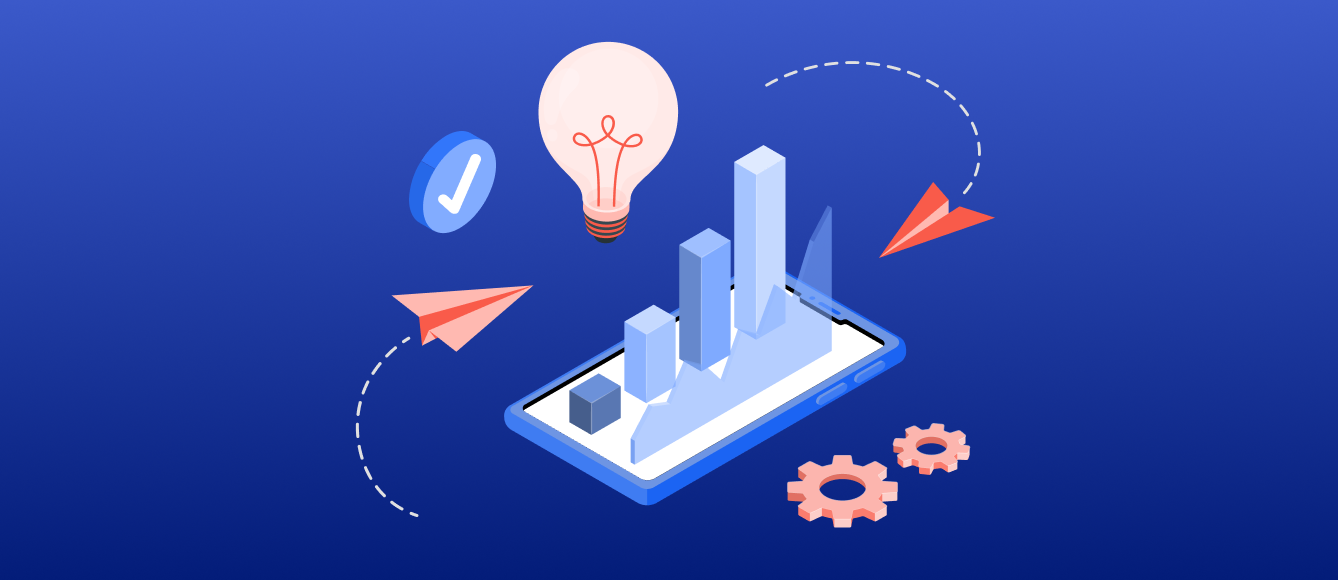
"*" indicates required fields